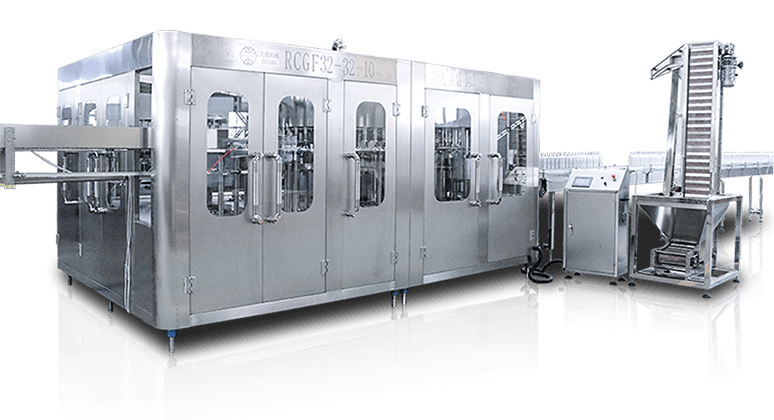
Washing Head | 14 |
Filling Head | 12 |
Capping Head | 5 |
Total Power ( kw ) | 3 |
Weight ( kg ) | 2200 |
Overall DIM( mm ) | 2050*1550*2200 |
Suitable Bottle Shape | Circular or Square | Machine Operator | 1 |
Bottle Diameter(mm) | Φ50-Φ95 | Cap Elevator | Anti-gravity Belt Lifter |
Bottle Height(mm) | 150-310 | Cabinet | Independent Cabinet |
Bottle Volume | 0.2-2L | Electricals | Schneider |
Washing | Aseptic Water | Touch Screen / PLC / Inverter | Mitsubishi or Siemens |
Auxiliary Equipment | Water Treatment System/Bottle Blowing System/Labeling Machine/Date Printer/ Packing Machine/Conveyor System |
Washing Head | 16 |
Filling Head | 16 |
Capping Head | 6 |
Total Power ( kw ) | 3.5 |
Weight ( kg ) | 2800 |
Overall DIM( mm ) | 2400*1750*2200 |
Suitable Bottle Shape | Circular or Square | Machine Operator | 1 |
Bottle Diameter(mm) | Φ50-Φ95 | Cap Elevator | Anti-gravity Belt Lifter |
Bottle Height(mm) | 150-310 | Cabinet | Independent Cabinet |
Bottle Volume | 0.2-2L | Electricals | Schneider |
Washing | Aseptic Water | Touch Screen / PLC / Inverter | Mitsubishi or Siemens |
Auxiliary Equipment | Water Treatment System/Bottle Blowing System/Labeling Machine/Date Printer/ Packing Machine/Conveyor System |
Washing Head | 18 |
Filling Head | 18 |
Capping Head | 6 |
Total Power ( kw ) | 4 |
Weight ( kg ) | 3000 |
Overall DIM( mm ) | 2550*1850*2200 |
Suitable Bottle Shape | Circular or Square | Machine Operator | 1 |
Bottle Diameter(mm) | Φ50-Φ95 | Cap Elevator | Anti-gravity Belt Lifter |
Bottle Height(mm) | 150-310 | Cabinet | Independent Cabinet |
Bottle Volume | 0.2-2L | Electricals | Schneider |
Washing | Aseptic Water | Touch Screen / PLC / Inverter | Mitsubishi or Siemens |
Auxiliary Equipment | Water Treatment System/Bottle Blowing System/Labeling Machine/Date Printer/ Packing Machine/Conveyor System |
Washing Head | 24 |
Filling Head | 24 |
Capping Head | 8 |
Total Power ( kw ) | 5.5 |
Weight ( kg ) | 4500 |
Overall DIM( mm ) | 3000*2150*2200 |
Suitable Bottle Shape | Circular or Square | Machine Operator | 1 |
Bottle Diameter(mm) | Φ50-Φ95 | Cap Elevator | Anti-gravity Belt Lifter |
Bottle Height(mm) | 150-310 | Cabinet | Independent Cabinet |
Bottle Volume | 0.2-2L | Electricals | Schneider |
Washing | Aseptic Water | Touch Screen / PLC / Inverter | Mitsubishi or Siemens |
Auxiliary Equipment | Water Treatment System/Bottle Blowing System/Labeling Machine/Date Printer/ Packing Machine/Conveyor System |
Washing Head | 32 |
Filling Head | 21 |
Capping Head | 10 |
Total Power ( kw ) | 7.5 |
Weight ( kg ) | 6000 |
Overall DIM( mm ) | 4200*2700*2400 |
Suitable Bottle Shape | Circular or Square | Machine Operator | 1 |
Bottle Diameter(mm) | Φ50-Φ95 | Cap Elevator | Anti-gravity Belt Lifter |
Bottle Height(mm) | 150-310 | Cabinet | Independent Cabinet |
Bottle Volume | 0.2-2L | Electricals | Schneider |
Washing | Aseptic Water | Touch Screen / PLC / Inverter | Mitsubishi or Siemens |
Auxiliary Equipment | Water Treatment System/Bottle Blowing System/Labeling Machine/Date Printer/ Packing Machine/Conveyor System |
Washing Head | 40 |
Filling Head | 40 |
Capping Head | 12 |
Total Power ( kw ) | 11 |
Weight ( kg ) | 9000 |
Overall DIM( mm ) | 4700*3200*2400 |
Suitable Bottle Shape | Circular or Square | Machine Operator | 1 |
Bottle Diameter(mm) | Φ50-Φ95 | Cap Elevator | Anti-gravity Belt Lifter |
Bottle Height(mm) | 150-310 | Cabinet | Independent Cabinet |
Bottle Volume | 0.2-2L | Electricals | Schneider |
Washing | Aseptic Water | Touch Screen / PLC / Inverter | Mitsubishi or Siemens |
Auxiliary Equipment | Water Treatment System/Bottle Blowing System/Labeling Machine/Date Printer/ Packing Machine/Conveyor System |
Washing Head | 50 |
Filling Head | 50 |
Capping Head | 15 |
Total Power ( kw ) | 15 |
Weight ( kg ) | 15000 |
Overall DIM( mm ) | 6500*3350*2400 |
Suitable Bottle Shape | Circular or Square | Machine Operator | 1 |
Bottle Diameter(mm) | Φ50-Φ95 | Cap Elevator | Anti-gravity Belt Lifter |
Bottle Height(mm) | 150-310 | Cabinet | Independent Cabinet |
Bottle Volume | 0.2-2L | Electricals | Schneider |
Washing | Aseptic Water | Touch Screen / PLC / Inverter | Mitsubishi or Siemens |
Auxiliary Equipment | Water Treatment System/Bottle Blowing System/Labeling Machine/Date Printer/ Packing Machine/Conveyor System |
Washing Head | 60 |
Filling Head | 60 |
Capping Head | 15 |
Total Power ( kw ) | 20 |
Weight ( kg ) | 18000 |
Overall DIM( mm ) | 7200*3650*2600 |
Suitable Bottle Shape | Circular or Square | Machine Operator | 1 |
Bottle Diameter(mm) | Φ50-Φ95 | Cap Elevator | Anti-gravity Belt Lifter |
Bottle Height(mm) | 150-310 | Cabinet | Independent Cabinet |
Bottle Volume | 0.2-2L | Electricals | Schneider |
Washing | Aseptic Water | Touch Screen / PLC / Inverter | Mitsubishi or Siemens |
Auxiliary Equipment | Water Treatment System/Bottle Blowing System/Labeling Machine/Date Printer/ Packing Machine/Conveyor System |
The rotary wheel is a fully SUS304 stainless steel welded structure.
The machine applies unique overturning bottle clamp, which is an innovation of our company. This bottle clamp grips bottle at neck position, avoiding bottle mouth thread contamination caused by rubber gripper block of a traditional bottle clamp. Made of SS304 stainless steel, this bottle clamp is hygienic and durable.
The high efficiency atomizing spray nozzle installed on bottle clamp incorporating technology from Spaying Systems Co. Ltd., is capable of cleaning any part of bottle inner wall, and also saves rinsing water.
The rinse is driven by driving system positioned inside machine frame via gear transmission.
The filler is designed and manufactured with application of Italy technology, providing hardware guarantee for securing product quality and reducing loss.
Rotary wheel are fully made of stainless steel SS304.
Filling valves are designed and manufactured with German technology, made of SS304, featuring high filling accuracy and high filling speed.
Bottles are raised and lowered by cam controlled lifting cylinder. Valve opening mechanism is actuated by air cylinder.
Hydraulic pump is float-ball controlled.
The filler is driven by driving system positioned inside machine frame via gear transmission.
The capper is most precise part in 3 in 1 filling machine, because the quality of machine is important to running credibility and product quality. The sealing machine in our company has strongpoint as follows:
The cover track has the device to prevent the reversal cover from passing and pick out the reversal cover. Meanwhile the photoelectric switch can stop the machine automatically when there is no cover on the track, by which it can avoid bottle without cover effectively.
It also has the bottle check-up switch. Together with cylinder on the joint of the cover track and cover lift, they can control the cover flow and stop it in case no bottle to reduce the quantity of cover.
Highly effective acentric way for cap sorting to reduce the abrasion.
It has the check-up device to control the cover lift.